ABANA Members in Action
Science and Smithing with Robb Gunter
Robb Gunter was presented with a Bealer Award at ABANA’s 50th Anniversary Celebration & Blacksmithing Conference in June 2024. The Bealer Award is bestowed in recognition of outstanding service to the blacksmith community and is the most prestigious award given by ABANA. Well known for developing “Super Quench,” Robb has spent decades perfecting his craft, demonstrating, and teaching others. He was an early advocate for ABANA’s educational programs. He continues to run Robb Gunter Architectural Metals in New Mexico, focusing on high-end architectural, sculptural, and decorative work.
Origin Story
I have always been interested in Blacksmithing. As a young boy, I would watch Gun Smoke in hopes of seeing the blacksmithing on the show.
I was already working at Sandia National Laboratories doing aircraft metal work when I found out about a man in Santa Fe (Rolando DeLeon) who taught a class in traditional blacksmithing. I was hooked. Shortly after, I was blessed to meet Francis Whitaker, Tom Joyce, Frank Turley, Clay Spencer, and others who were always willing to share information and techniques that helped me to become a better smith.
While working at Sandia National Laboratories in the precision metal forming section, I began to introduce the idea of forgings as a viable and economical way to produce prototype parts. From 1976 to 1993, I worked at Sandia National Laboratories, spending 13 of those years as the Resident Blacksmith.
During my tenure, I developed what is known amongst blacksmiths as the Super Quench, a heat-treating solution for mild and low carbon steels, and with Karl Schuler developed the Recuperative Gas Forge. Over 2,000 of them have been built around the country [and plans are still available here].
Architectural Work
I’ve always liked architecture and studied art all through school so architectural smithing was a perfect fit. I’ve always delighted in a challenge, and the fit-up and technical problem solving in railings, chandeliers, and door hardware was a perfect match.
My favorite thing to forge is large chandeliers. Several of the large commissions have had numerous chandeliers in them. I always delighted in working with my two sons on the projects. The largest commission took all 3 of us 22 months to complete.
One of the most fun projects is the Old European fireplace front [pictured]. The client had me study fireplaces in castles and estates in Europe and design one that would be compatible with all the antique European furniture in their home. It took 6 weeks to complete.
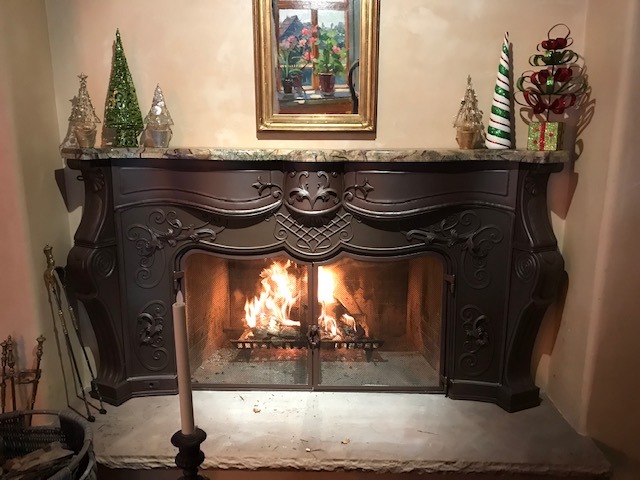
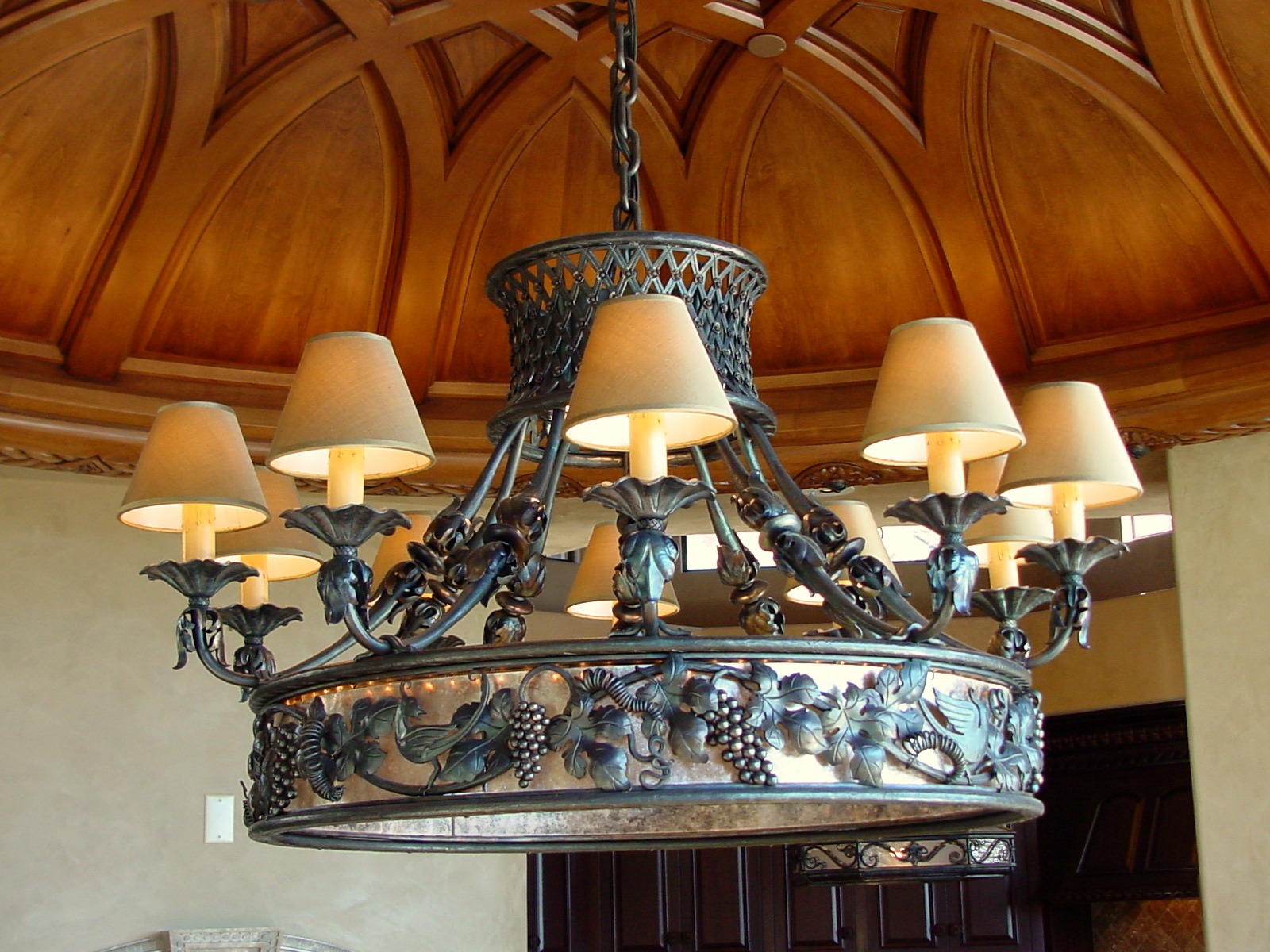
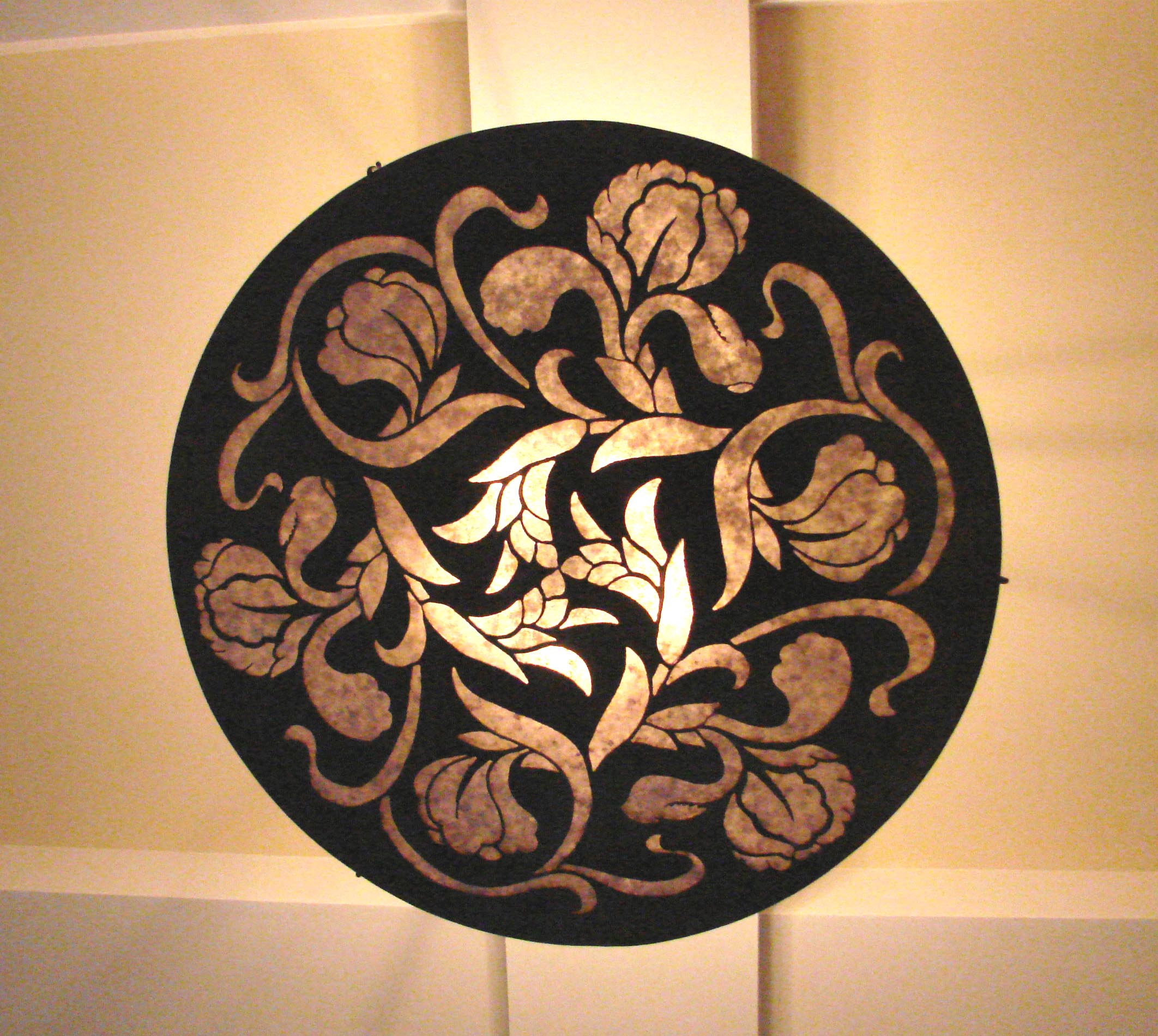
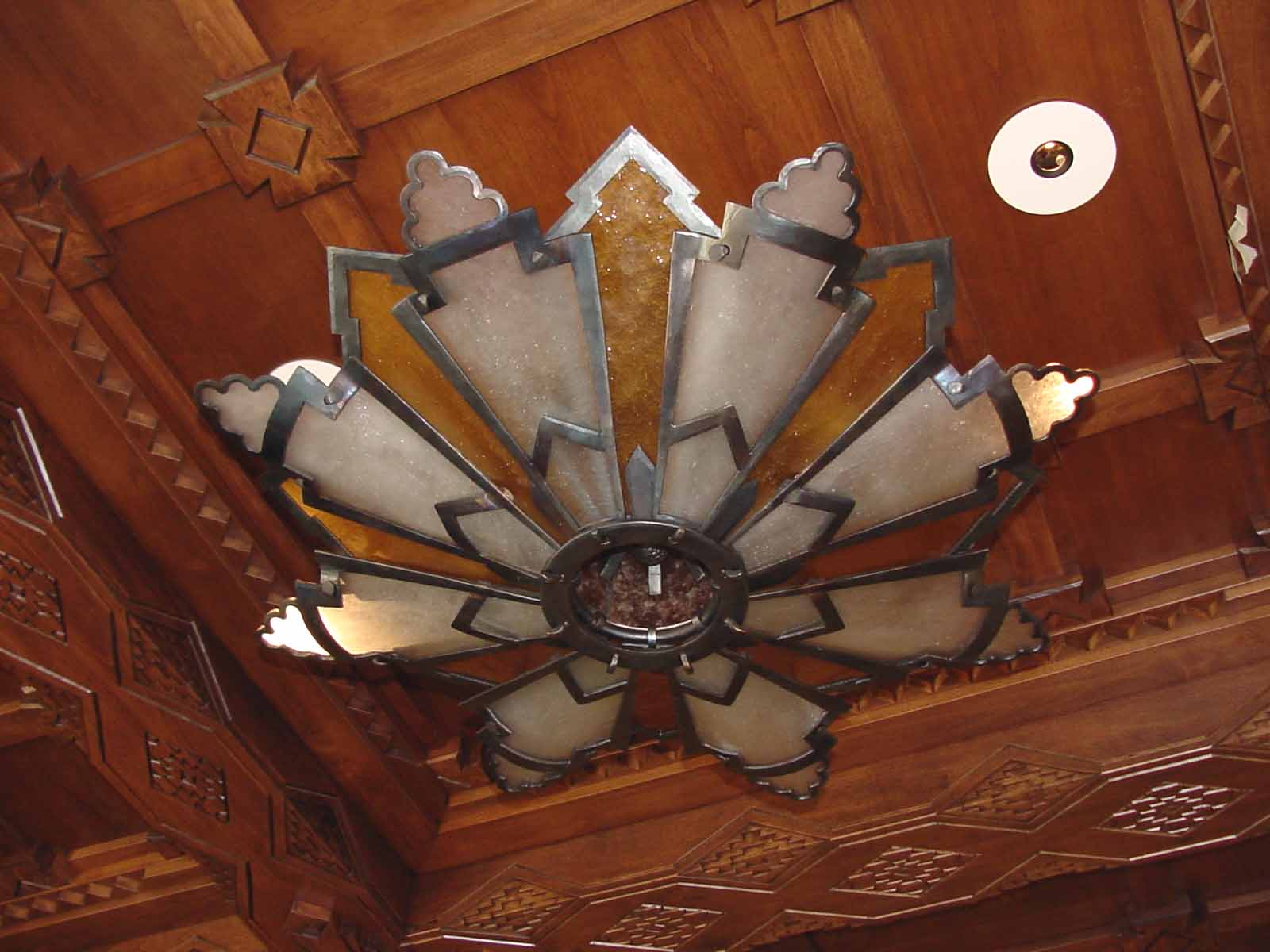
From G-Man to Entrepreneur
The move from working at the laboratory to private commission work was part of a 10-year plan my wife and I had. We had re-arranged our financial situation to enable the move. We had built a new shop, which included a school facility for six students at a time. I had been building up my client list all the while. I had already taught classes in traditional blacksmithing on nights and weekends for seven years before I took the leap. Walking away from the “Golden Handcuffs” was frightening but so worth it.
I’ve been self-employed now for 31 years and have loved every minute of it. Francis Whitaker told me early on that if I would turn out nothing but the highest quality I was capable of, people would beat the door down to get to me. He was certainly right.
Special Moments
Working as the smith at Sandia National Laboratories for 13 out of the 17 years that I was there was an amazing opportunity. It allowed me to forge and gain experience with all kinds of materials that I couldn’t even think of affording. Getting to forge exotic aro-space materials, platinum titanium, and other very strange stainless steel alloys that were being developed at the Labs was a great learning experience.
Both of my sons started smithing at age five and worked at the forge exhibit at the New Mexico State Fair at that age. As they grew into men and continued to work at the forge, they both considerably passed me in skill. It was always a blessing to work with them. They always came up with innovative approaches and fixtures that I’d never have thought of. They taught me a lot.
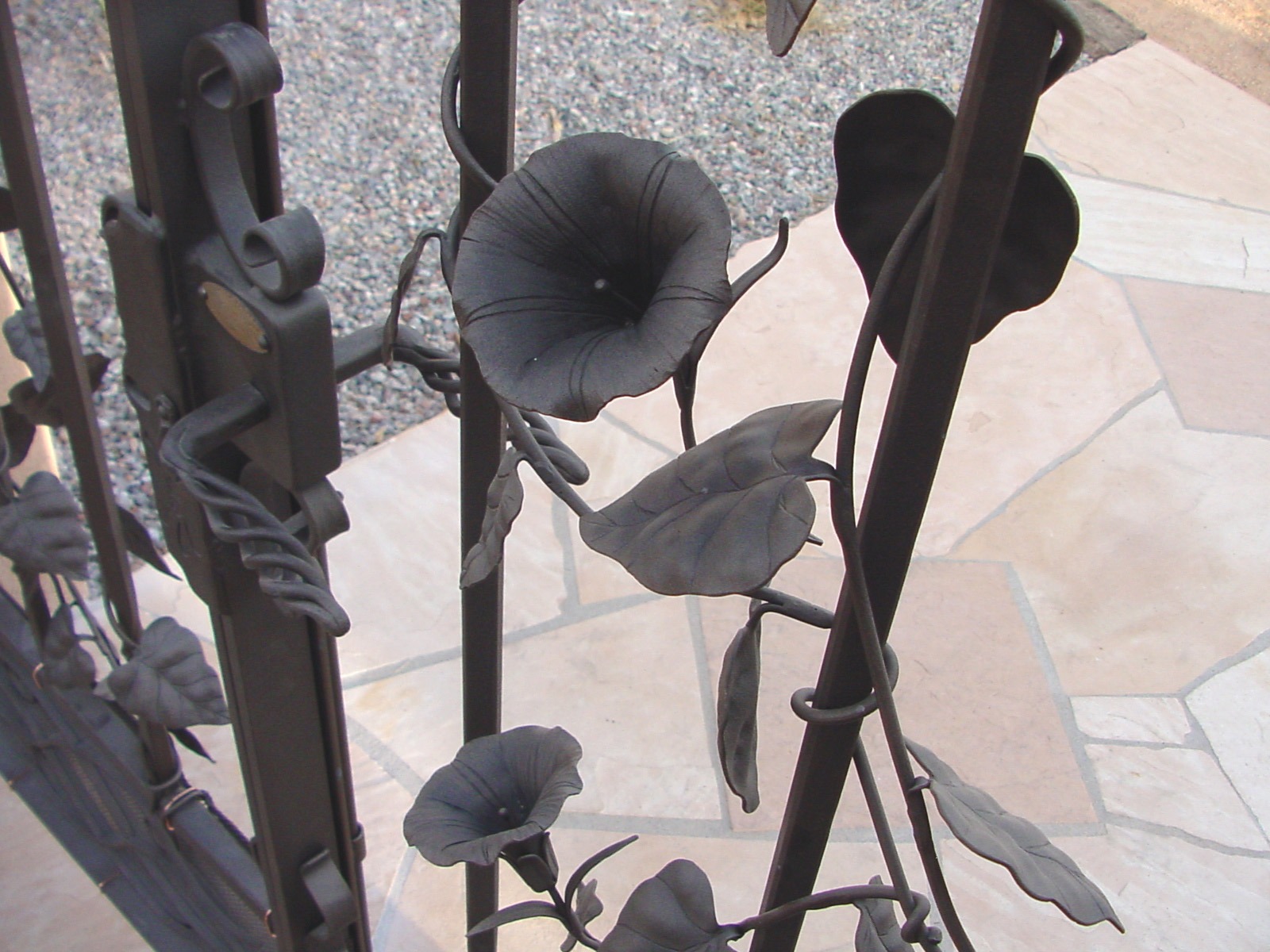
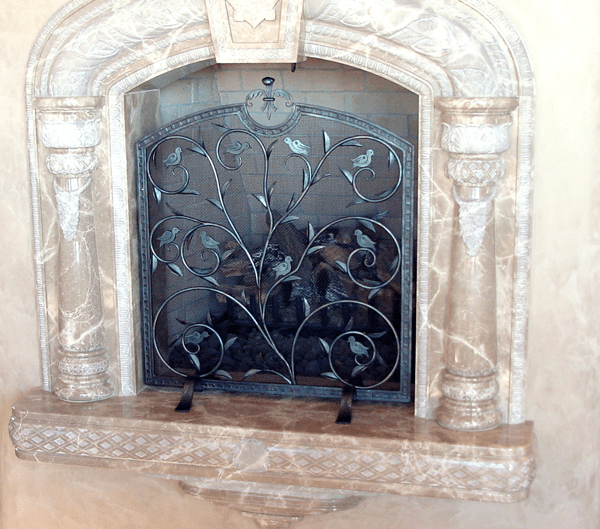
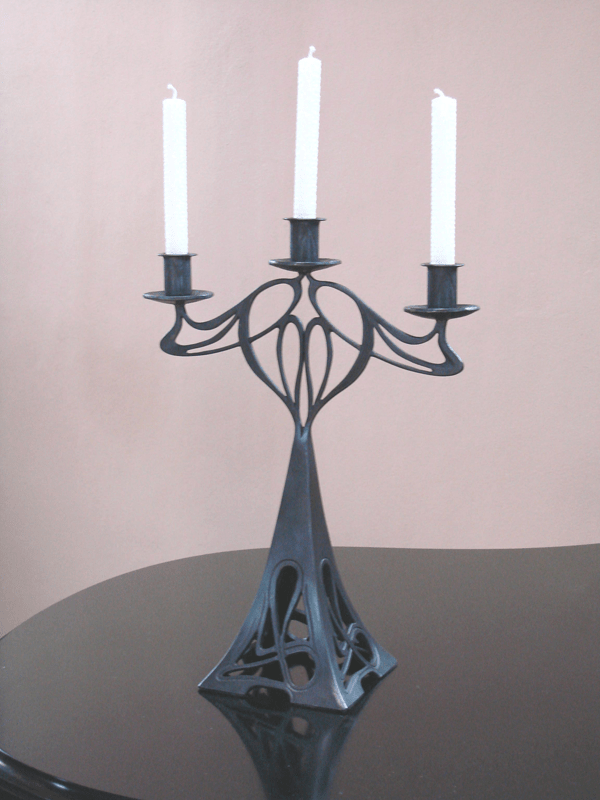
Recommended Reading
Probably one of the most valuable books to me is Otto Schmirler’s “Work and Work Methods of The Artist Blacksmith”—not so much for the style but for the tooling and jig ideas.
Advice for Budding Blacksmiths
Practice, practice, practice!! Build a diverse blacksmithing library, and study every style of forge work. Get to every conference and workshop you can, and always be willing to share what you have learned. No one is born a blacksmith. Francis always said, “The life so short, the craft so long to learn.” Never stop learning!!
Do you know an ABANA member with an interesting story to tell or project to discuss? Drop us a line at socialmedia@abana.org and we’ll take it from there! They might be featured on our ABANA Members in Action page.